As a consumer, we are sure you have faced this situation where you loved a product, but either it was out of stock, or your size was unavailable. This can be a big drawback for the companies when they can’t provide the products to their customers. The products that are out of stock are called the finished goods inventory in the business terminology.
It is essential for businesses to properly manage their finished goods inventory to ensure that their stock does not run out and they can provide to all their customers. If you want to know what finished goods inventory is, how it works, and how to calculate it, we have you covered. In this article, we have mentioned everything that you need to know. So, let’s jump right into the article.
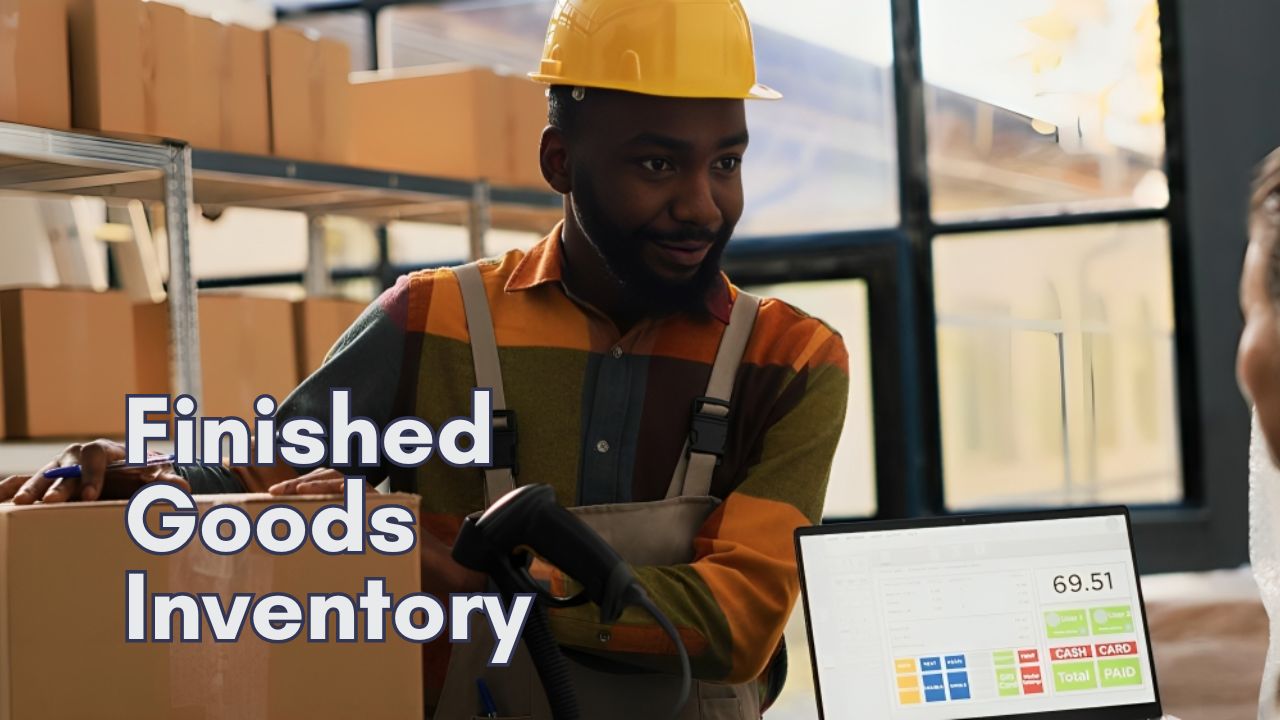
Part 1. What is the Finished Goods Inventory?
Finished goods inventory can be defined as the total stock companies make and is available for the customers to purchase. These products are ready for vendors, retailers, and consumers. This relative term does not mean finished or completely processed products.
These finishes can become raw materials for the buyers—one simple example is a company producing silk or cotton for the brands. Cotton and silk can be the finished products for the company producing them, but for the brands, they are the primary raw materials through which they will make the clothes for their customers.
Part 2. How to Calculate Finished Goods Inventory?
The next question that might come is how to calculate finished goods inventory. There is a proper finished goods inventory formula that you can use to calculate it.
Finished goods = [COGM – COGS] + previous finished goods inventory value
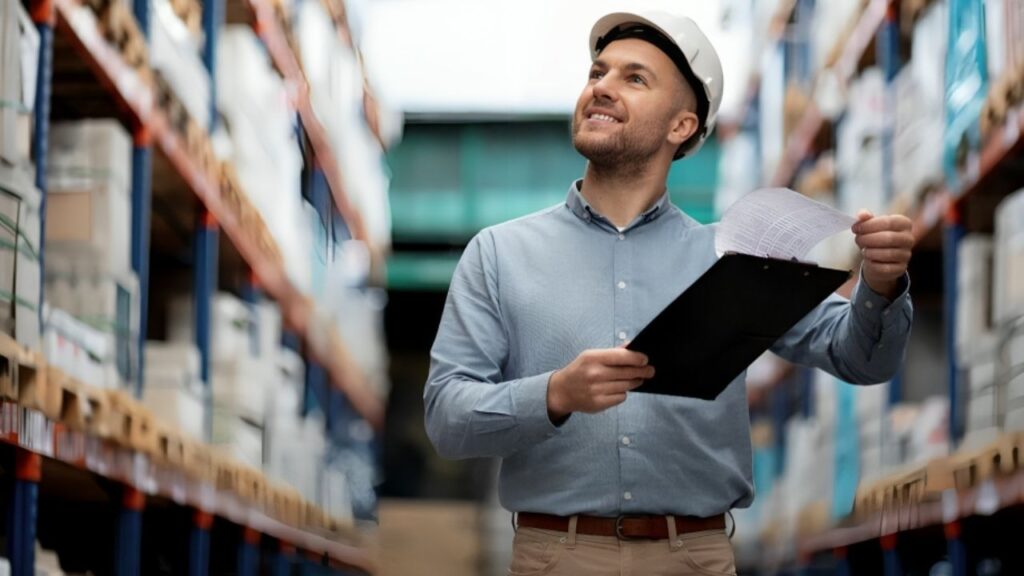
Here, you need to know the cost of goods manufactured (COGM) and the costs of goods sold (COGS). These values should be of the same period to get the most accurate answer.
For calculating COGM, there is another formula that you should use. Following is the formula that is needed.
[beginning WIP inventory + total manufacturing cost] – ending WIP inventory
For calculating COGS, the following is the formula you need to use.
[beginning inventory + purchases during the period] − ending Inventory
Once you have calculated COGS and COGM, you can simply put those values in the finished goods inventory formula, add the previous finished goods inventory value, and you will have the value of your present finished goods.
Example of Finished Goods Inventory
Now that you know the finished goods inventory formula, we have an example to clarify this concept better. For example, you are a business making cups, and last year, you produced about 1000 cups and sold them for $5. Calculating the previous year’s finished inventory would be 1000 x $5= $5000. For this year, your company produced 1,200 cups and sold them for $5.
This year, you were able to sell 700 cups. So, if you calculate the COGM, it will be 1200 x $5= $6000; if you calculate the COGS, it will be 700 x $5= $3500. Now, adding these values to the finished goods inventory formula, you need to subtract COGS from COGM, giving you $2500. Now, you need to add the value of the previous year’s finished goods inventory, which was $5000. The final value will be $2500 + $5000= $7500. This means your finished goods inventory is worth about $7500.
Part 3. Why Finished Goods Inventory is Important
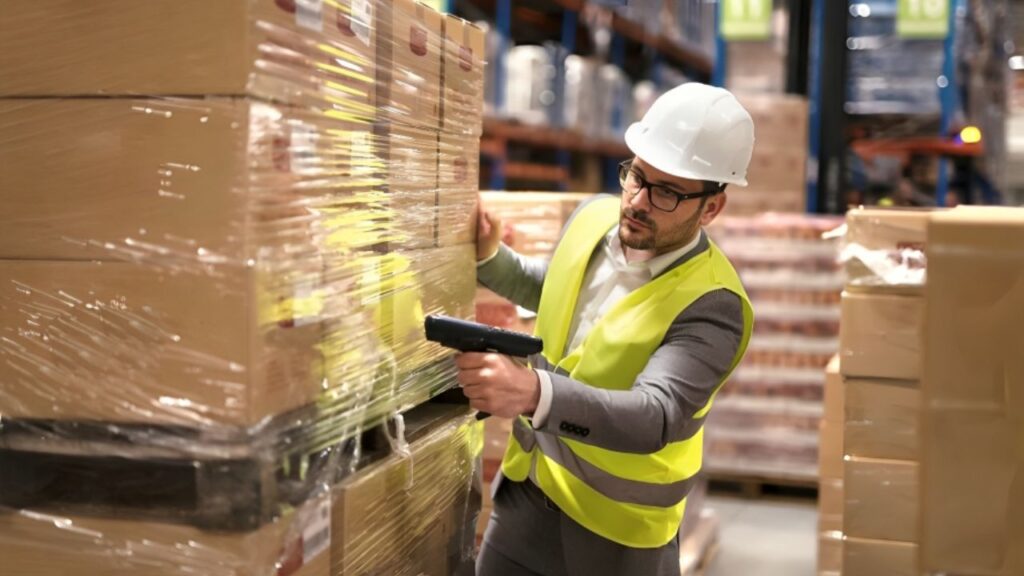
You might wonder why it is essential and why business owners must calculate this value. For successful manufacturing, businesses must know this. By keeping track of the finished inventory, the company will know how much stock they have in their inventory, allowing them to better understand how many items they need to produce.
This is also very important for the business to follow the trends and manage the sales fluctuations. You also need to know the finished inventory to improve the financial budgeting. You can order the balance sheets and financial statements to maintain the current assets. When you know your finished inventory, you will be able to manage other parts of our business; you can create budgets accordingly and manage the manufacturing of the items accordingly.
Knowing the inventory levels will also ensure you reduce the waste material without spending over on your products. If you have an excessive amount of inventory and keep on producing it, you will waste a lot of your products at the end of the day.
This is why you must keep proper track of the inventory and the number of finished goods you have; if you don’t keep a record, you will face many losses, which can hurt your business.
Part 4. How NextSmartShip Help Improve Finished Goods Inventory Management?
Managing the inventory is very important and quite challenging because there are so many things that you need to keep track of. This is why NextSmartShip is here to help you. They are one of the best companies to help you manage your inventory. They can also help with taking orders from customers, ensuring that the proper packaging is done, and delivering the products to the customers.
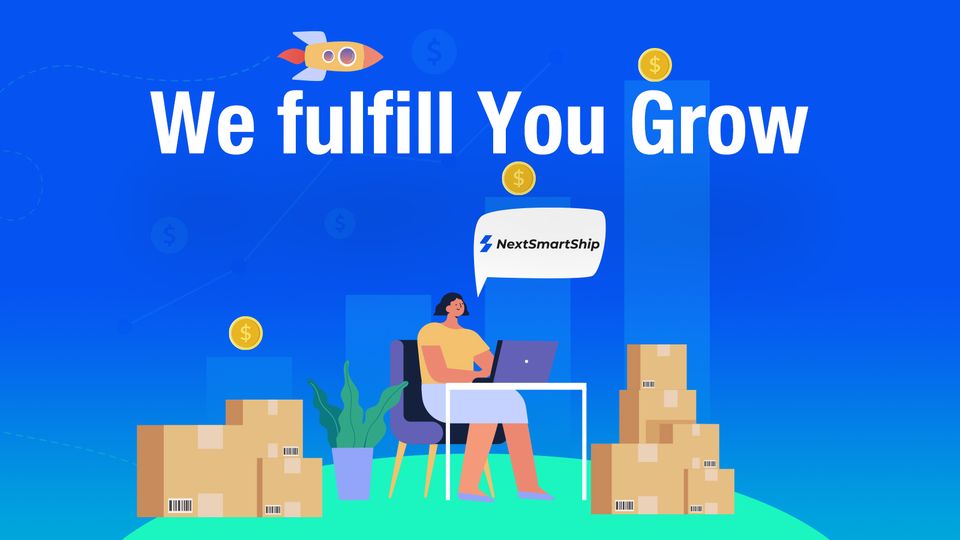
This makes it very easy for the business to leave the inventory in the hands of NextSmartShip and focus on other parts of the company, such as marketing, promotions, and simply growing the company more.
Conclusion
There are a lot of things that you need to manage when you are running a business. Among these different things, you also need to ensure you have enough stock so that you can cater to all your customers. The stock that you have is called the finished goods inventory, and it becomes very crucial that you manage this inventory. Hence, we hope this article was beneficial for you in learning what a finished goods inventory is and how to calculate it.
If it becomes very hectic for the business to keep track of the inventory, you must check NextSmartShip because they will help you manage your inventory efficiently.